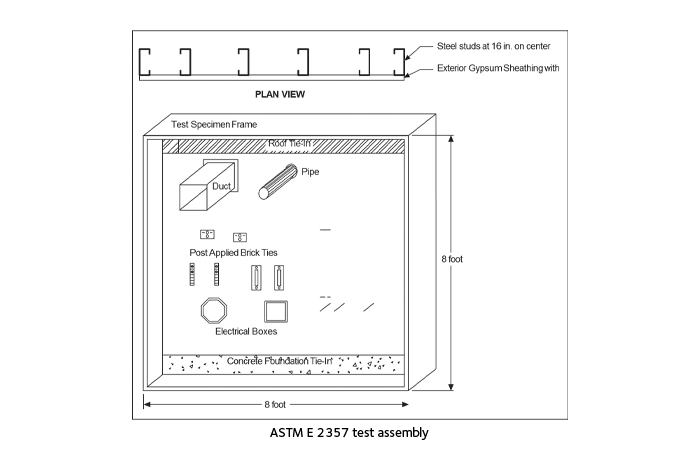
No architect or building engineer today would consider erecting a commercial building without a continuous, fully adhered air barrier system. The need to eliminate or control air infiltration/exfiltration through wall assemblies in order to maximize energy efficiency and prevent moisture problems is well recognized throughout the industry. For more than four decades, GCP has led the development and continued innovation of air barrier technologies with its PERM-A-BARRIER® family of wall membrane systems.
A brief history
While a continuous air barrier is a standard component of building walls today, this was not always the case. Back in the 1960s and 1970s, most buildings were erected with no air barrier. Often, asphalt-saturated felt paper was used simply as a water-resistive barrier (WRB). By the 1980s, concerns about energy conservation and materials durability—and increased awareness of the role of air infiltration in building health and efficiency—led to new standards for air barriers.
In 1985, Canada introduced air barrier requirements in the National Building Code of Canada (NBCC), specifying that “…the assembly shall be designed to provide an effective barrier to air exfiltration and infiltration, at a location that will prevent condensation within the assembly.” Architects in the United States took note and started specifying air barriers. Some U.S. states instituted their own requirements, such as section 1304.3.1 of the Massachusetts building code, which requires a continuous air barrier from foundation to roof to control air leakage.
Early air barrier products did not fully live up to the goal of preventing air leakage, however. While spun polyolefin building wraps mechanically attached to the sheathing became common, their limitations soon became apparent. They did not provide a truly continuous barrier, allowing air leakage at seams and joints. In addition, they were often damaged or dislodged when exposed to the elements prior to the installation of cladding.
To address this issue, some innovative architects and construction contractors started applying to wall assemblies an adhesive, sheet-applied product with proven waterproofing properties. That product was BITUTHENE® Post-Applied Waterproofing developed by GCP, still one of the most widely used waterproofing membranes in the world. This provided a continuous, durable membrane with strong adhesive properties. But it was not specifically engineered to control air movement through wall assemblies.
GCP leads the way
During the 1980s GCP introduced the first PERM-A-BARRIER® wall membrane. It provided a first-of-its-kind solution for architects and builders seeking a purpose-built, sheet-applied, impermeable air barrier that was easy to install and provided a continuous, fully adhered membrane.
At the time, there were no established industry standards for air barriers—or for evaluating their performance. GCP played a key role in helping shape these standards, working with leading standards organizations.
In 2005, GCP contributed to the development of ASTM E 2357, a standardized test designed to assess an air barrier assembly’s ability to resist air leakage in simulated real-world conditions. Prior to the introduction of ASTM E 2357, standardized tests evaluated only individual components of the air barrier assembly—the air barrier product alone, flashing or sealing materials. But this approach does not provide the information needed to understand how these components will perform together within the building envelope. By contrast, the ASTM E 2357 test is conducted using full-size mock-ups of wall assemblies with typical materials and penetrations. The test is designed to evaluate how the components work together to prevent air leakage. To be considered an effective air barrier system, air permeability (leakage) must not exceed 0.04 cfm/ft2 under a pressure differential of 75 Pa.
PERM-A-BARRIER® liquid, vapor permeable and sheet-applied air barrier products have been independently tested in accordance with to ASTM E 2357. All maintained air permeance less than 0.0008 cfm/ft2 under conditions specified by the standard. After successfully completing the ASTM E 2357 testing, the air barrier assemblies were subjected to extreme wind loading, the equivalent of 168 mph wind gusts. The wall structure was brought to failure before the air barrier allowed leakage.
Performance in the field
GCP air barrier technology has also proven itself in field testing. In 2013 Syracuse University and Oak Ridge National Laboratory conducted a long-term evaluation comparing a GCP fully adhered air barrier to a mechanically attached membrane using a full-sized mockup of a house in upstate New York. Initial air leakage was measured and sensors monitored the temperature, humidity, moisture, and heat changes through four seasons. After 16 months, air leakage was remeasured and the cladding was removed to inspect the condition of the air barriers.
At the initial measurement, the mechanically attached air barrier had 562% more air leakage than the fully adhered GCP system. At the conclusion of the 16 months, air leakage through the mechanically attached membrane showed an 83% increase—978% more than the GCP system. In addition, the mechanically attached barrier showed damage, while the fully adhered GCP barrier was in perfect condition.
Since its introduction, the PERM-A-BARRIER® system has been used in thousands of commercial building projects around the world and continues to perform as designed. This 40-plus-year track record, unique in the air barrier industry, speaks to the intelligent engineering of the original product.
Expanding capabilities
As building science has advanced, GCP has continued to develop its air barrier offering with innovations designed to expand PERM-A-BARRIER® system capabilities and benefits.
GCP pioneered the liquid-applied, impermeable air barrier membrane product. This enabled rapid installation of continuous air barriers on walls with uneven surfaces and/or with a high number of penetrations. Applied by spray or roller, PERM-A-BARRIER® liquid dramatically accelerated the process of installing an effective, continuous air barrier.
In the early 2000s, GCP was among the first to introduce a vapor permeable air barrier. This increased the versatility of the system, offering designers more flexibility in the positioning of the air barrier within the wall assembly. PERM-A-BARRIER® vapor permeable membranes allows the diffusion of moisture in the form of vapor, enabling building walls to “breathe” while still maintaining a building envelope that resists air leakage and rain penetration. Ultimately, GCP offered vapor permeable membranes in both sheet-applied and liquid-applied products.
GCP was also first to market with the PERM-A-BARRIER® aluminum wall membrane. This fully bonded, impermeable, aluminum-faced membrane protects the building superstructure from the damaging effects of the elements, while enhancing the thermal performance of the structure. This innovation was soon imitated by GCP competitors.
Installation breakthroughs
GCP was a leader in developing air barrier innovations designed to simplify and speed installation by contractors. The company was among the first to introduce a primerless air barrier, eliminating a step required by many sheet-applied membranes. Our primerless PERM-A-BARRIER® product featured a new, more aggressive adhesive that bonds strongly to a variety of substrate materials without requiring a primer. In ASTM D4541 pull-off testing, the primerless product achieved an impressive 20 psi strength. In fact, this product required the GCP R&D team to develop a new release liner that would peel off this new, more aggressive adhesive.
Other innovations focused on expanding the climatic conditions under which air barriers could be installed. GCP developed a primerless air barrier designed to be installed in temperatures down to 25° F. In colder climates, this dramatically expanded the installation window into the winter months.
Rain presents a problem for conventional liquid-applied air barriers, which must remain dry until cured. Even a light rain could ruin the membrane, requiring costly and time-consuming re-application. GCP developed a rain-resistant, liquid-applied membrane designed to adhere and cure in light rain conditions. This innovation helps avoid project delays in climates where sudden, brief showers are common and frequent.
Fire resistance performance
Reducing the risk to building occupants posed by fire is a high priority when designing building envelopes. In 1998, the National Fire Protection Agency (NFPA) developed its NFPA 285 standard, defining a test method for determining the flammability characteristics of exterior, non-load-bearing wall assemblies containing combustible materials.
GCP air barriers have all been tested in accordance with ASTM E1354-17, a standard test method that uses an oxygen consumption calorimeter to determine the ignitability, heat release rates, mass loss rates, effective heat of combustion, and visible smoke development of materials. GCP was an early adopter of this standard to assess air barrier performance in NFPA 285—a practice that is now common among air barrier suppliers. GCP performs such tests on a variety of wall assembly configurations. This is crucial, as changes to any component in the wall assembly can change the test results.
Continued evolution
While the original PERM-A-BARRIER® sheet-applied air barrier remains unchanged—due to customer demands for a solution they trust without reservation—the PERM-A-BARRIER® family of products continues to evolve to meet changing needs.
PERM-A-BARRIER® VPL liquid-applied product and PERM-A-BARRIER® VPS 30 and NPS sheet-applied products have been refined to deliver the same performance with less thickness (25mil vs. 40mil for the liquid product and as low as 18mil for the sheet product). Using less material helps support GCP’s sustainability goals, reducing our carbon footprint—and those of our customers and building owners. Yet in independent tests, performance continues to meet the high standards set by our original formulation.
With temperatures reaching record highs in many parts of the world today, thermal performance is increasingly critical. GCP’s PERM-A-BARRIER® VPL 50RS UV stable, vapor permeable barrier can be exposed for up to 12 months, allowing flexibility in scheduling. The product’s thermal performance has been tested up to 300° in-service temperature. This high-temp stability helps address the challenge posed by sunlight reflectivity from adjacent buildings, which can dramatically increase wall temperatures even in temperate climates.
GCP continues to devote significant investments in its PERM-A-BARRIER® products to anticipate and meet the challenges facing architects, contractors and building owners. A number of GCP innovations were or still are protected by patent rights, including:
• US8277915B2 for a self-adhered, vapor permeable, easy-to-install air barrier membrane.
• US10487218B2 for a fire retardant, vapor impermeable, environmentally friendly coating composition.
• US8524822B2 for a vapor permeable, liquid-applied membrane.
• US8748528B2 for a vapor-permeable barrier coating for low temperature application.
• US11072716B2 for a sag-resistant vapor permeable barrier coating applicable at low temperature.
A systems approach
Like any system, an air barrier is only as good as its weakest point. This recognition drives GCP’s total system approach to optimizing air barrier performance.
All PERM-A-BARRIER® products are developed as components of a single, integrated system comprising membrane, wall flashing, detail membrane, sealant, and (if required) primer. All system components have been tested extensively to validate compatibility. This ensures that the membrane will adhere well not only to the substrate, but to the membrane itself at critical interfaces, such as laps and penetrations—not just on the day of installation, but over the life of the building.
The people behind the products
A key advantage of air barrier products is the team of chemists and building scientists behind the products. Some of the same professionals who developed our groundbreaking—and still industry-leading—BITUTHENE® waterproofing products played a leading role in developing our PERM-A-BARRIER® products.
GCP further assures its customers’ success through the company’s world-class technical support. GCP product technical experts are available to address any questions regarding product selection, performance testing, installation, or any other customer concern. If needed, GCP experts can provide support on-site.
A proven track record
Commercial buildings represent tremendous financial investments and, in some cases, even represent a company’s brand and reputation. Optimizing every aspect of building performance is critical to maximize return on investment—and minimize the risk to building occupants and owners alike. A continuous, fully adhered air barrier is an essential element to prolong the life of the structure, protect occupant health, improve energy efficiency, and support sustainable building practices.
For more than 40 years, PERM-A-BARRIER® has set the standard for air barrier innovation, performance and durability. Our comprehensive portfolio of fully bonded air barrier products have been proven in halo commercial buildings on multiple continents and in diverse climates. When you specify a PERM-A-BARRIER® permeable or impermeable, sheet-applied or liquid-applied air barrier, you are taking an important step in assuring the success of your project for many years to come.
Learn more and find a GCP sales contact or distributor at gcpat.com
Tags
- Air & Vapor Barriers
- BITUTHENE
- Building Envelope Solutions
- PERM-A-BARRIER
- PREPRUFE